Melhores Práticas para Manutenção de Automação Industrial
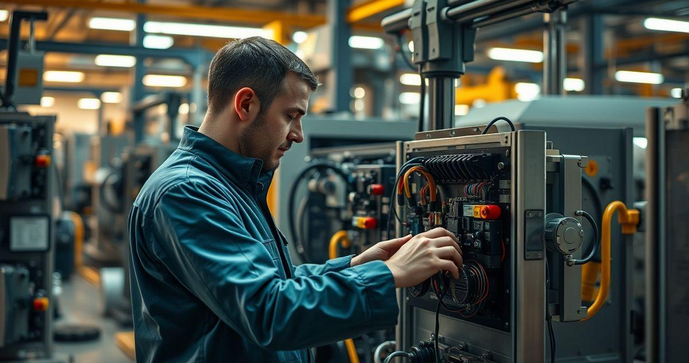
Por: Ingrid - 27 de Maio de 2025
Importância da Manutenção Proativa na Automação Industrial
A manutenção proativa na automação industrial é uma abordagem estratégica que visa prevenir falhas e otimizar o desempenho dos equipamentos. Diferentemente da manutenção reativa, que se concentra em corrigir problemas após eles ocorrerem, a manutenção proativa antecipa possíveis falhas e implementa ações corretivas antes que afetem o funcionamento da linha de produção.
Essas práticas têm um impacto significativo na continuidade operacional, reduzindo o tempo de parada e aumentando a disponibilidade dos sistemas automatizados. Ao identificar e corrigir problemas potenciais durante inspeções regulares, as indústrias podem maximizar a eficiência e minimizar custos operacionais associados a quebras inesperadas.
Além disso, a manutenção proativa contribui para a segurança no ambiente de trabalho. Ao evitar falhas inesperadas, diminui-se o risco de acidentes que podem resultar do mau funcionamento de máquinas ou equipamentos. Investir em um programa de manutenção proativa é, portanto, um passo fundamental para garantir não só a eficácia dos processos, mas também a segurança dos colaboradores.
Os benefícios são evidentes: a redução de custos com reparos emergenciais, a extensão da vida útil dos equipamentos e a melhoria na qualidade dos produtos. Também é importante destacar que, com os dados coletados durante as manutenções, as empresas podem fazer análises preditivas. Isso permite um planejamento mais eficaz das operações e um melhor gerenciamento dos recursos disponíveis.
Por fim, a manutenção proativa se alinha com as tendências modernas de Indústria 4.0, onde a integração de tecnologias avançadas, como IoT e Big Data, permite monitorar continuamente o desempenho dos equipamentos e ajustar as estratégias de manutenção em tempo real. Portanto, adotar uma abordagem proativa não é apenas uma boa prática; é uma necessidade para as indústrias que buscam se manter competitivas no mercado atual.
Principais Métodos de Manutenção em Sistemas Automatizados
Os principais métodos de manutenção em sistemas automatizados incluem uma variedade de abordagens que visam garantir a operação contínua e eficiente dos equipamentos. Cada método tem suas características, vantagens e objetivos específicos, e optar pelo adequado pode fazer a diferença entre operações bem-sucedidas e falhas indesejadas.
1. Manutenção Corretiva: Este método envolve a execução de reparos ou substituições após a ocorrência de uma falha. Embora seja uma abordagem comum, pode resultar em tempos de inatividade mais longos e custos elevados. Utilizada geralmente em sistemas menos críticos, a manutenção corretiva é uma solução reativa.
2. Manutenção Preventiva: Refere-se a ações planejadas e programadas para evitar falhas antes que ocorram. Com base em intervalos de tempo ou uso, a manutenção preventiva pode incluir inspeções regulares, limpezas e substituições de peças. Essa abordagem é eficaz para prolongar a vida útil dos equipamentos e minimizar paradas inesperadas.
3. Manutenção Preditiva: Utilizando tecnologias avançadas, como sensores e monitoramento em tempo real, a manutenção preditiva analisa as condições operacionais para prever falhas antes que elas ocorram. Isso permite intervenções mais eficientes e programadas, baseadas em dados reais de desempenho. O uso de técnicas como análise de vibração e termografia ajuda a identificar problemas potenciais sem comprometer a atividade produtiva.
4. Manutenção Proativa: Este método combina elementos da manutenção preventiva e preditiva, focando na identificação e eliminação de causas raízes de falhas antes que se tornem eventos críticos. Adotar uma abordagem proativa envolve realizar análises e planejamentos cuidadosos, visando uma melhoria contínua na eficiência operacional.
5. Manutenção Inteligente: Integrada às tendências da Indústria 4.0, a manutenção inteligente faz uso de tecnologias como IoT e Machine Learning para criar sistemas que aprendem em tempo real e automatizam processos de manutenção. Esses sistemas são capazes de otimizar automaticamente as rotinas de manutenção, melhorando a gestão de ativos e a confiabilidade do equipamento.
Em resumo, a escolha do método de manutenção adequado para sistemas automatizados é essencial para garantir a eficiência, segurança e continuidade das operações. A combinação de diferentes abordagens pode resultar em uma estratégia robusta que maximize o desempenho e a vida útil dos sistemas industriais, minimizando custos operacionais e riscos associados a falhas.
Ferramentas e Tecnologias para Manutenção Eficiente
A adoção de ferramentas e tecnologias adequadas é fundamental para garantir uma manutenção eficiente em sistemas automatizados. Com o avanço da tecnologia, diversas soluções têm sido desenvolvidas para otimizar processos de manutenção, aumentar a eficiência e reduzir custos operacionais.
1. Sistemas de Gestão de Manutenção Assistida por Computador (CMMS): Essas plataformas são essenciais para o planejamento e a rastreabilidade de atividades de manutenção. Elas permitem programar tarefas, acompanhar ordens de serviço, gerenciar inventários de peças de reposição e analisar o desempenho dos equipamentos. Com um CMMS, as equipes de manutenção podem maximizar a eficiência e melhorar a tomada de decisão por meio de dados históricos e análises.
2. Monitoramento por IoT: Os dispositivos de Internet das Coisas (IoT) são cada vez mais utilizados para monitorar equipamentos em tempo real. Sensores conectados coletam dados sobre funcionamento, temperatura, vibração e outros parâmetros relevantes que ajudam a prever falhas. Esses dados podem ser usados para realizar manutenções preditivas e otimizar o ciclo de vida dos ativos.
3. Análise de Dados e Big Data: A análise de grandes volumes de dados gerados pelos sistemas industriais é crucial para a implementação de estratégias de manutenção eficientes. Ferramentas de análise de dados podem transformar os dados coletados em informações valiosas, permitindo que as empresas identifiquem padrões, tendências e áreas de melhoria. Isso contribui para otimizar os processos de manutenção e reduzir custos.
4. Realidade Aumentada (AR) e Realidade Virtual (VR): Essas tecnologias estão sendo exploradas para treinar equipes de manutenção e auxiliar em atividades complexas. A AR pode fornecer sobreposições visuais de informações diretamente sobre o equipamento durante as manutenções, facilitando a identificação de problemas e a execução de reparos. Já a VR pode ser utilizada para simulações de treinamento em ambientes virtuais, permitindo que os técnicos pratiquem suas habilidades sem riscos reais.
5. Manutenção Móvel: Aplicativos móveis voltados para manutenção oferecem acesso remoto a informações de equipamentos e ordens de serviço. Isso permite que as equipes de manutenção acessem dados em tempo real, registrem problemas e atualizações diretamente no local de trabalho, aumentando a eficiência e agilidade na resposta a eventuais falhas.
6. Impressão 3D: A impressão 3D vem ganhando espaço na fabricação de peças sob demanda, reduzindo os tempos de espera por peças de reposição. Essa tecnologia permite que as empresas mantenham um inventário reduzido e se ajustem rapidamente a necessidades específicas, minimizando períodos de paradas não programadas.
Em suma, a integração dessas ferramentas e tecnologias nas rotinas de manutenção não apenas melhora a eficácia dos processos, mas também contribui para a competitividade das empresas no mercado. A adoção de soluções inovadoras é um passo crucial para garantir uma manutenção eficiente e alinhada às demandas da Indústria 4.0.
Erros Comuns na Manutenção de Automação e Como Evitá-los
A manutenção de automação industrial é crucial para garantir a eficiência operacional e a segurança dos processos. No entanto, muitos profissionais cometem erros que podem comprometer a eficácia das atividades de manutenção. Identificar esses erros comuns e entender como evitá-los é fundamental para otimizar o desempenho. A seguir, apresentamos alguns dos principais erros e dicas para prevenção.
1. Falta de Planejamento Adequado: Um dos erros mais frequentes é a ausência de um planejamento claro para as atividades de manutenção. Sem um cronograma bem definido, as equipes podem perder prazos importantes e negligenciar tarefas essenciais. Para evitar isso, estabeleça um plano de manutenção que inclua inspeções regulares, ações preventivas e um banco de dados com o histórico de manutenções realizadas.
2. Ignorar a Documentação Técnica: Muitas falhas ocorrem porque os técnicos não consultam a documentação dos equipamentos. Manuais, diagramas e registros são recursos vitais para a execução correta de manutenções. Para prevenir esse erro, garanta que a documentação esteja sempre acessível e que a equipe seja treinada para utilizá-la adequadamente.
3. Realizar Manutenção sem Treinamento Adequado: A falta de capacitação adequada pode resultar em execuções imprecisas e na não identificação de problemas críticos. Invista em treinamentos regulares para sua equipe, abordando não só manutenções gerais, mas também atualizações sobre novas tecnologias e procedimentos. Essa iniciativa ajuda a garantir que todos estejam preparados para enfrentar os desafios compartilhados durante a manutenção.
4. Negligenciar a Segurança: Em ambientes industriais, a segurança deve ser sempre uma prioridade. Muitos erros ocorrem quando se descuida de medidas de segurança ao realizar manutenções. É fundamental seguir os protocolos de segurança e utilizar equipamentos de proteção pessoal (EPIs) adequados. Instruir a equipe sobre os riscos e práticas seguras é essencial para manter um ambiente de trabalho seguro.
5. Ignorar Sinais de Alertas de Falhas: É comum que técnicos ignorem sinais de problemas nos equipamentos, como ruídos estranhos ou desempenho irregular. Esses sinais são indicadores de que algo pode estar errado. Para evitar a subestimação desses sinais, implemente rotinas de monitoramento e incentivo para que as equipes relatem imediatamente quaisquer anomalias observadas.
6. Dependência Excessiva de Manutenção Corretiva: Algumas indústrias ainda adotam a estratégia de esperar que um problema ocorra antes de agir. Essa abordagem pode resultar em custos elevados e ineficiência. Troque a manutenção corretiva excessiva por um modelo que priorize a manutenção preventiva e preditiva, para minimizar riscos e otimizar a utilização do equipamento.
7. Falta de Comunicação entre Equipes: A falta de comunicação entre as equipes de manutenção e operação pode levar a mal-entendidos que resultam em falhas. Estabeleça canais de comunicação claros e rotinas que promovam a troca de informações entre as equipes, garantindo que todos estejam atualizados sobre as condições dos equipamentos.
Em resumo, evitar os erros comuns na manutenção de automação industrial requer planejamento, treinamento, e um compromisso contínuo com as práticas de segurança e comunicação. Ao adotar medidas proativas, as empresas podem garantir um desempenho mais eficiente e seguro, contribuindo para a sustentabilidade das operações industriais.
Impacto da Manutenção na Produtividade Industrial
A manutenção de automação industrial exerce um papel vital na produtividade de uma fábrica. A forma como as empresas gerenciam suas atividades de manutenção pode ter um impacto direto na eficiência operacional e, consequentemente, na capacidade de produção.
1. Redução de Paradas Não Programadas: Quando a manutenção é realizada de forma eficaz, as paradas não programadas são minimizadas. Equipamentos que operam continuamente sem interrupções tendem a produzir mais e atender melhor à demanda do mercado. Manutenções preventivas e preditivas permitem que as empresas identifiquem problemas antes que se transformem em falhas, garantindo a continuidade da produção.
2. Aumento da Vida Útil dos Equipamentos: Investir em uma boa estratégia de manutenção não apenas evita falhas, mas também prolonga a vida útil dos equipamentos. Com uma vida útil mais longa, as empresas podem evitar custos significativos de substituição e aproveitar ao máximo seus ativos, contribuindo assim para uma produção mais eficiente.
3. Melhoria da Qualidade do Produto: A manutenção adequada dos maquinários e sistemas automatizados impacta diretamente na qualidade dos produtos finais. Equipamentos bem mantidos operam com precisão, resultando em menos defeitos e retrabalhos. Isso não só preserva a satisfação do cliente, mas também reduz desperdícios e aumenta a eficiência da linha de produção.
4. Otimização do Uso de Recursos: Um bom planejamento de manutenção permite às empresas gerenciar melhor os seus recursos, sejam eles humanos ou materiais. Ao evitar paradas e falhas inesperadas, os operadores podem focar na produção e no atendimento aos clientes em vez de se preocuparem com reparos emergenciais.
5. Aumento da Moral da Equipe: Ambientes de trabalho onde equipamentos funcionam eficientemente tendem a elevar a moral da equipe. Quando os colaboradores não precisam lidar com máquinas quebradas ou interrupções constantes, tornam-se mais produtivos e engajados no trabalho. Isso contribui para um ambiente positivo e colaborativo.
6. Capacidade de Resposta ao Mercado: Em um cenário industrial em constante mudança, a capacidade de adaptação é crucial. Manutenções bem planejadas permitem que as empresas respondam rapidamente às mudanças na demanda. Equipamentos sempre prontos para produção possibilitam ajustes rápidos, aumentando a competitividade da empresa.
Portanto, a relação entre manutenção e produtividade industrial é clara. A eficácia das atividades de manutenção influencia diretamente a eficiência operacional, qualidade do produto, e satisfação da equipe. As empresas que priorizam boas práticas de manutenção estão mais bem posicionadas para prosperar em um mercado altamente competitivo.
Tendências Futuras em Manutenção de Automação Industrial
À medida que a automação industrial continua a evoluir, as tendências de manutenção também se transformam para se adaptar às novas tecnologias e demandas de mercado. As empresas que adotam essas tendências não apenas melhoram sua eficiência operacional, mas também se posicionam competitivamente no cenário industrial. A seguir, apresentamos as principais tendências futuras em manutenção de automação industrial.
1. Manutenção Baseada em Dados: A coleta e análise de dados em tempo real estão se tornando cruciais para a manutenção eficiente. O uso de tecnologias como Big Data e Inteligência Artificial permite que as empresas analisem grandes volumes de informações para prever falhas e otimizar processos. Esse avanço reduz custos e melhora a tomada de decisão em relação à manutenção.
2. IoT e Manutenção Conectada: A Internet das Coisas (IoT) envolve a interconexão de equipamentos e dispositivos, permitindo que máquinas se comuniquem e compartilhem dados. Isso oferece insights valiosos sobre o desempenho e a saúde dos ativos, possibilitando uma abordagem mais proativa e agendada nas estratégias de manutenção, conforme a condição real dos equipamentos.
3. Adoção de Realidade Aumentada (AR): A realidade aumentada está começando a ser utilizada no suporte à equipe de manutenção. Ao fornecer informações visuais e instruções diretamente sobre o equipamento em tempo real, a AR melhora a eficiência e a precisão dos técnicos, permitindo diagnósticos mais rápidos e reparos mais eficientes.
4. Automação da Manutenção: A automação em processos de manutenção está se tornando cada vez mais comum. Isso inclui o uso de robôs e sistemas automatizados para realizar tarefas de manutenção, como inspeções e reparos. Essa abordagem não apenas economiza tempo, mas também reduz erros humanos e melhora a segurança nas operações.
5. Foco em Sustentabilidade: Com a crescente preocupação com o meio ambiente, há um movimento em direção a práticas de manutenção sustentáveis. Isso envolve o uso de materiais ecológicos, otimização de recursos e redução de desperdícios nas atividades de manutenção. As empresas que incorporam essas práticas não apenas atendem a exigências regulatórias, mas também melhoram sua imagem corporativa.
6. Treinamento Contínuo e Desenvolvimento de Habilidades: À medida que as tecnologias progridem, o papel dos profissionais de manutenção também se transforma. Os trabalhadores precisarão de formação contínua para se manterem atualizados sobre as novas ferramentas e métodos. Investir em treinamento e desenvolvimento de habilidades criará uma força de trabalho mais capaz e preparada para os desafios futuros.
Em suma, as tendências futuras em manutenção de automação industrial refletem uma transformação para maior eficiência, segurança e sustentabilidade. Adotar essas tendências pode proporcionar uma vantagem competitiva significativa e preparar as empresas para o futuro dinâmico da indústria.
A manutenção de automação industrial desempenha um papel essencial na eficiência e competitividade das empresas. Ao reconhecer a importância da manutenção proativa e adotar as melhores práticas e tecnologias disponíveis, as indústrias podem minimizar falhas, melhorar a qualidade do produto e aumentar a produtividade.
As tendências futuras indicam um movimento em direção à conectividade, automação e uso inteligente de dados, oferecendo novas oportunidades para otimização e sustentabilidade. Ao integrar essas abordagens, as empresas não apenas garantem seu funcionamento eficaz, mas também se preparam para os desafios e demandas do mercado em constante evolução.